Get consistent results with professional plastic extrusion techniques
Get consistent results with professional plastic extrusion techniques
Blog Article
Understanding the Essentials and Applications of Plastic Extrusion in Modern Manufacturing
In the realm of modern manufacturing, the method of plastic extrusion plays a crucial duty. Deciphering the basics of this procedure exposes the real convenience and potential of plastic extrusion.
The Principles of Plastic Extrusion Process
While it may appear complicated, the basics of the plastic extrusion process are based on reasonably simple concepts. It is a manufacturing process in which plastic is thawed and afterwards shaped into a continuous account with a die. The raw plastic material, typically in the form of pellets, is fed right into an extruder. Inside the extruder, the plastic goes through warmth and stress, creating it to thaw. The liquified plastic is after that compelled with a shaped opening, understood as a die, to develop a long, constant product. The extruded product is cooled down and then cut to the wanted size. The plastic extrusion process is thoroughly made use of in various industries due to its cost-effectiveness, performance, and versatility.
Different Kinds Of Plastic Extrusion Methods
Structure upon the standard understanding of the plastic extrusion process, it is essential to check out the different techniques involved in this production technique. In contrast, sheet extrusion develops big, level sheets of plastic, which are normally more refined right into items such as food packaging, shower curtains, and cars and truck parts. Comprehending these methods is essential to making use of plastic extrusion efficiently in modern production.

The Duty of Plastic Extrusion in the Automotive Market
An overwhelming bulk of parts in modern vehicles are products of the plastic extrusion procedure. This process has revolutionized the vehicle sector, transforming it into an extra reliable, cost-efficient, and flexible production market. Plastic extrusion is largely utilized in the production of various automobile components such as bumpers, grills, door panels, and control panel trim. The procedure provides an uniform, consistent outcome, allowing suppliers to create high-volume get rid of excellent accuracy and marginal waste. The lightness of the extruded plastic components adds to the general reduction in vehicle weight, improving fuel performance. The resilience and resistance of these parts to warmth, cold, and impact enhance the long life of automobiles. Hence, plastic extrusion plays a critical function in automotive manufacturing.

Applications of Plastic Extrusion in Customer Product Production
Beyond its significant effect on the auto sector, plastic extrusion shows equally effective in the realm of durable goods manufacturing. This procedure is crucial in developing a vast range of from this source products, from food product packaging to family devices, playthings, and also medical devices. The adaptability of plastic extrusion enables makers to develop and produce complex sizes and shapes with high precision and efficiency. Due to the recyclability of several plastics, extruded components can be reprocessed, decreasing waste and expense (plastic extrusion). The flexibility, flexibility, and cost-effectiveness of plastic extrusion make it a preferred choice for many customer items suppliers, adding substantially to the industry's development and technology. Nevertheless, the environmental implications of this prevalent usage require cautious factor to consider, a topic to be discussed additionally in the subsequent area.
Ecological Impact and Sustainability in Plastic Extrusion
The pervasive usage of plastic extrusion in manufacturing welcomes analysis of its ecological implications. As a procedure that regularly makes use of non-biodegradable materials, the environmental effect can be substantial. Energy usage, waste manufacturing, and carbon exhausts are all concerns. Industry improvements are boosting sustainability. Efficient equipment minimizes power usage, while waste management systems recycle scrap plastic, lowering resources demands. In addition, the development of eco-friendly plastics supplies an extra eco-friendly alternative. Despite his explanation these renovations, further technology is required to minimize the environmental impact of plastic extrusion. As society leans towards sustainability, manufacturers should adapt to remain viable, highlighting the value of constant research study and innovation in this field.
Conclusion
In final thought, plastic extrusion plays a vital role in modern manufacturing, specifically in the auto and consumer items industries. Recognizing the essentials of this process is crucial to maximizing its applications and benefits.
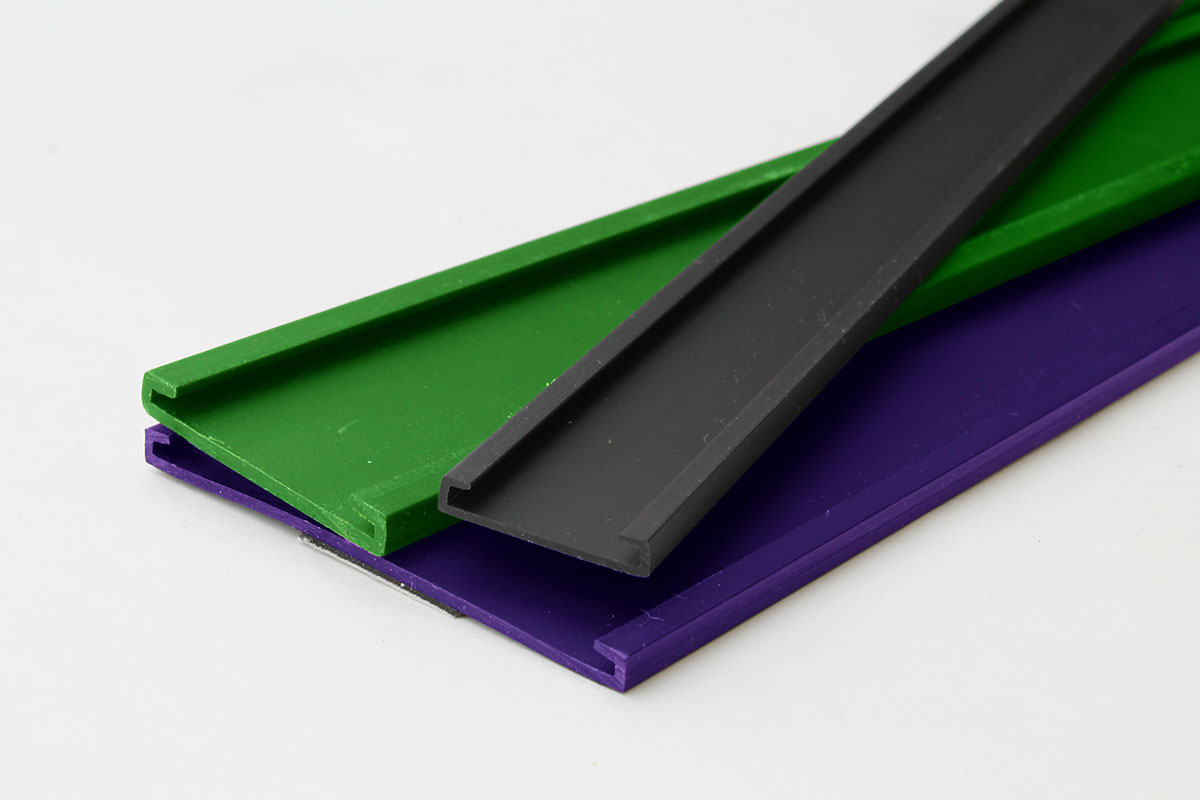
The plastic extrusion process is thoroughly used in different markets due to its effectiveness, cost-effectiveness, and adaptability.
Structure upon the see this site standard understanding of the plastic extrusion procedure, it is essential to discover the different techniques entailed in this manufacturing approach. plastic extrusion. In comparison, sheet extrusion creates large, flat sheets of plastic, which are normally additional processed into products such as food product packaging, shower drapes, and automobile parts.An overwhelming bulk of components in contemporary cars are items of the plastic extrusion process
Report this page